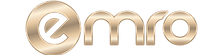
Materials Management
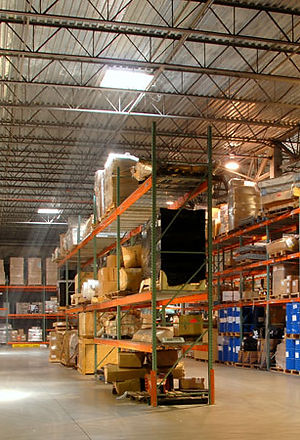
Customer (Sales) Orders
Whether reducing the amount spares in inventory or just facilitating a spare to another carrier, you can accurately track any method of trading with this Module. With Rental Orders, you can lend your spares using industry standards. The Exchange Outs are there if you have a shop that does 3rd Party work and you customarily send out serviceable units in exchange for unserviceable ones. Finally, Sales Orders are used to sell off your spares.
Other Customer Orders functionality includes:
● Serialized Unit Tracking
● Audit Trail of each transaction
● Return Unit Tracking
● Invoicing upon unit sales or return
● Multiple Rental Fee Factors by number of days
● Repair Cost tracking on Exchange Outs
● Ability to track & record Sales Returns & Refunds
Requisitions
The creation of requisitions can come from a number of sources: from technicians working on an aircraft or components, to Planning department personnel. Automatic reorder levels can be put in place to trigger an auto-reorder requisition when parts have reached their re-order level. This module also feeds the TRAX Dashboard geared for Management Graphical Reporting & Logistic Decision Support. At Login, Management need not navigate through detailed records; the Dashboard will quickly indicate the status of your AOG Requisitions, Fleet Status by Type/Series, Unscheduled Removals by Fleet, and more.
The following functionality is supported:
● Requisition authorization optional (by location and amount)
● Requisition by requirement: Aircraft, Work Order, or Site
● AOG requisitions will send automatic notes to specified personnel
● Audit trail on requisition changes
● Management of requisitions to allow redistribution of requirement
● Automatically receive messages sent for requisitions
● Ability to track aircraft defects with part requirements
● Requisition Assigned to Buyer report
● Requisition can be assigned to multiple orders
● Requisition for Kit will show kit build list required
● AOG Requisition message notifications can be sent to unlimited users with email option
Orders (TO,PO,RO++)
The Orders section deals with all order types on the system including sales, also from the beginning of the requirement (i.e. the basic requisition of parts).
The order types on the system are Contract Order, Exchange In/Out Order, Loan Order, Purchase Order, Service Order, Repair Order, Customer Order, Rental Order, Manufacturer Order, Warranty Claim Order, Transfer Order and Insurance Claim. Additional Order Module functions include, Order Status which allows for vendor interaction, Order Receiving Discrepancy to allow for Purchasing and Receiving Department interaction, Vendor Price Listing Import for data sources, and the Power by the Hour tracking capability.
Order authorization is an optional switch, which will allow users to have a financial level of authorization to enable control of the issue of orders and provides the option to have complete workflow capability for order approval.
SPEC2000 is supported for Quotations, Purchases, repairs, and invoicing.
Order Invoices can be registered on the system and information passed, via an appropriate interface, to the company’s financial systems.
Requisitions
The creation of requisitions can come from a number of sources: from technicians working on an aircraft or component, to the planning department personnel. Requisitions may automatically generate with Inventory Transactions as defined by Re-Order level requirements. These Re-Order Requisitions will notify Purchasing/ Materials Department when parts are diminishing and require replenishment.
As well as the normal query and report facilities, management graphical reporting is available.
Orders
Orders can be created and tracked on the system as required (including send via SPEC2000). Graphical explorer technology is used to give easy visibility of orders and their statuses.
There is considerable functionality associated with the orders section of the system. Other Orders functionalities include:
● Online history of all orders which feeds to the Requisition Module
● Quotation issue and tracking
● Vendor Performance Tracking
● Orders can be automatically reserved for a particular Work Order
● Repair Order entry includes component repair requirements, removal
information, and repair history
● Multiple Warranty controls
● Exchange Order Support with Order type conversion (i.e. RO to EX, EX to PO, etc.)
● Warehouse Transfer Order monitoring
● One Step Transfer Support
● Loan and Rental Orders with cost monitoring
● Contract Orders for automatic re-order POs issued to Preferred Vendor.
● Online Vendor performance statistics & recommendation
● Invoices can be pipelined to accounts payable system
The Orders section deals with all order types in the system except Part Sales, Exchange Outs, and Rentals, which are found in the Customer Orders Module.
Receiving
The Receiving module is part of the "Closed Loop System," which receives materials on one side and the Packing & Shipping module that sends out materials on the other side. This module is highly dependent on our Settings, Engineering, and Production modules since it is highly aware of all Serial Numbers and their history. Receiving knows not to allow receipt of a serial number in the bogus parts list and scrapped parts. It also knows if a part is returning from repair and prompts you for confirmation of compliance and entry of tear down reports. With Receiving Inspection, Inspectors sign off on the 2nd step of receiving for those parts that require it. There are workflow checklists for both Receivers & Inspectors to ensure proper receiving steps are being followed. Recalls are easily done with Batch Control Numbers assigned to each batch of parts received. Tool Calibration & Shelf Life is also initialized during this process.
Other Receiving functionalities include:
● Batch Control
● Assembly Receiving
● Hazmat Indicators
● Shelf Life Date-Stamp
● Tool Calibration Date-Stamp
● Workflow Checklist
● Approved Certificate Recording
● Form one or 8130 scanning
● Serviceable Tag Printing
● Tear Down Reporting
● Bin Control Features
Inventory
The Inventory module provides for complete control and management of aircraft and non-aircraft materials, serialized parts, non-serialized parts, and kits.
Standard transactions are provided for within the inventory section, such as Bin Transfer, Adjustments, Scraps, Manual Issues, Picklist Issues, Return to Stock, Return to Vendor, Exchange Issues, Loan Returns, Warehouse Transfers, Build/Break Kits, Rental Issues, Order queries, Requisition Creation, Tool Tracking, and more. With Packing/Shipping interface available for applicable items.
Reporting and query options are provided for Inventory, Inventory Transaction History, and Physical Inventory.
Other options include Manual Warranty Entry, P/N Initial Loading, P/N Reorder Level control, Physical Inventory Adjustment, Physical Inventory Count, and Picklist Creation.
This module feeds information to other modules and vice versa. For example, when a Work Order is created for an aircraft, the materials required can be reserved with warehouse reservation routing and picklists created and printed in stores. Any items that are issued from stores can be tracked on the Work Order system, allowing total cost based accounting.
Mobile inventory functions are available for picklists, issues, part query and others (using PDA or specialist equipment).
RFID functions are available for Tool check-in and check-out as well as stock receipts/issues/transfers and other functions.
Other Inventory functionalities include:
● Supports Multiple Locations
● Stock checking
● MSG-2/MSG-3 Rotable component tracking
● Picklists (manual or automatic) for In Stock Parts
● Requisitions (Separate Module) for Out of Stock Parts
● Material Reservation capabilities from Work Order based on Pre-Draw requirements
● Kit Building, Breaking, and Part Search shows parts within kits
● Decimal quantities for UOM
● Optional two stage receiving | inspection
● Stolen parts monitoring
● Returns to vendor
● Type/Series and aircraft tail effectivity on all part issues
● FIFO or LIFO on all parts
● Customer stock separation (consignment)
● Unlimited part types
● Batch tracking
● Packing and Shipping Documentation
● Airway bill tracking
● Financial accounting on all transactions
● Warranty Tracking
● Shelf Life Tracking
● Tool Calibration Tracking
● P/N Reorder Levels with optional Poisson Factor Auto-Recalculation
● Physical Inventory Counting
Picklists
The request for an IN-STOCK part is a Picklist. Whether it is a mechanic out in the Line, Hangar, or at the Store's Desk, he can request an inventory item. Planners and Production Managers can also generate a picklist for all the pre-draw parts listed in the Work Order from the click of a button. Stores receive the Picklists and work off of these.
Picklist Issues record the recipient's name and signature.
The Picklist Management screen allows Managers to work and manage these requests. A request for an out-of-stock part in the Picklist will prompt the user for the condition and direct them to a Requisition.
Packing & Shipping
This may be overkill but that is what's required by the Airlines and the industry's regulatory authorities. A "Closed Loop System," allows for checks and balances to ensure that information remains accurate. A mistake made by one user affects another in the loop. With Packing & Shipping, we close the loop on external Material movements and extend visibility of the Pack, Ship, and Track functionality offered by this module to buyers, material managers, and outstations.
Other Packing & Shipping functionalities include:
● Automatic grouping of Orders
● Quick Search Engine for Items awaiting shipment
● Airway Bill Tracking
● Packing Material Dimensions
● Hazmat Alerting with MSDS notes
● Customs Tracking capability
● Orders Module integration

HARMONY & RAGE
I'm a paragraph. Click here to add your own text and edit me. It’s easy. Just click “Edit Text” or double click me to add your own content and make changes to the font. Feel free to drag and drop me anywhere you like on your page. I’m a great place for you to tell a story and let your users know a little more about you. This is a great space to write long text about your company and your services. You can use this space to go into a little more detail about your company.

THE REAL STORY
I'm a paragraph. Click here to add your own text and edit me. It’s easy. Just click “Edit Text” or double click me to add your own content and make changes to the font. Feel free to drag and drop me anywhere you like on your page. I’m a great place for you to tell a story and let your users know a little more about you. This is a great space to write long text about your company and your services. You can use this space to go into a little more detail about your company.